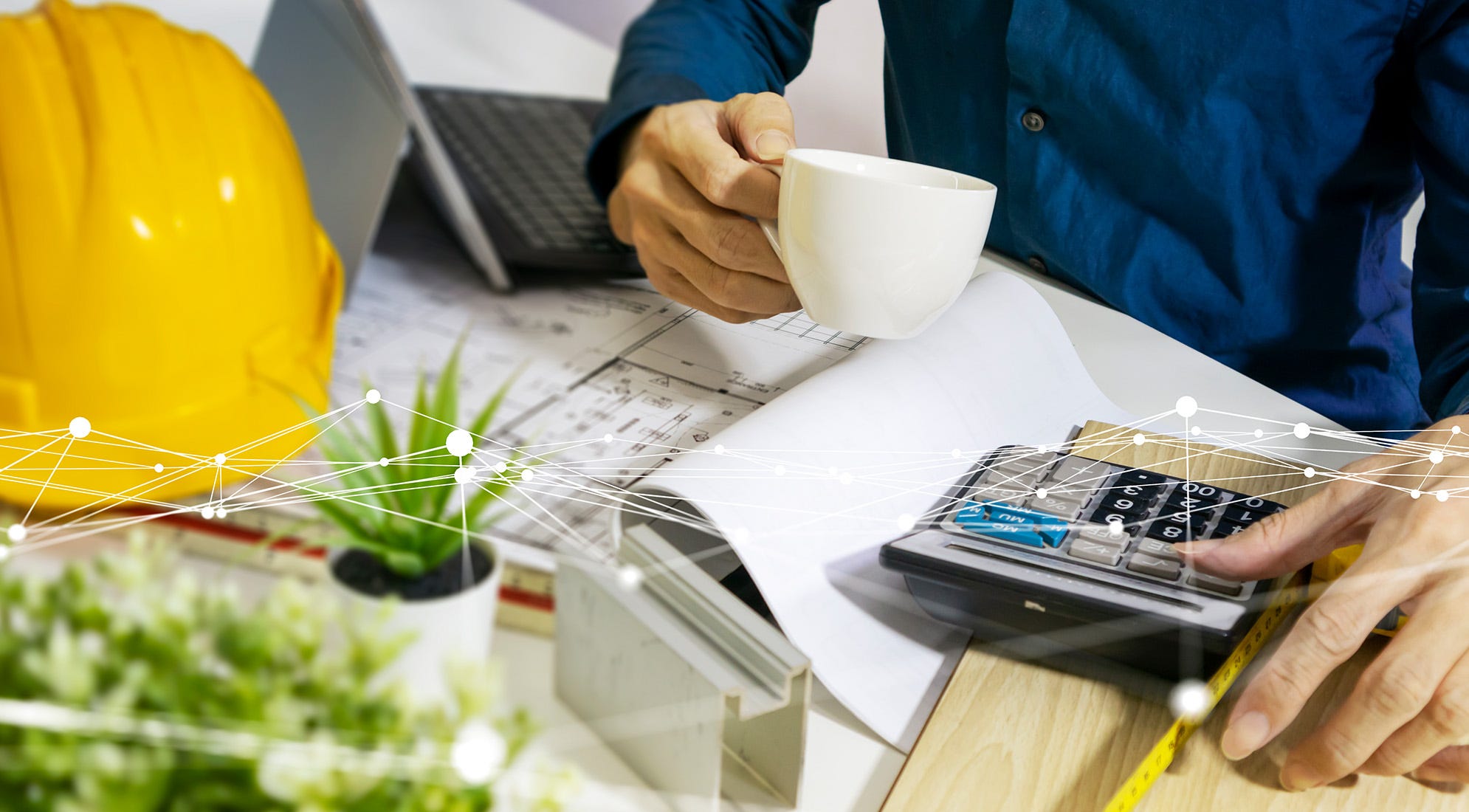
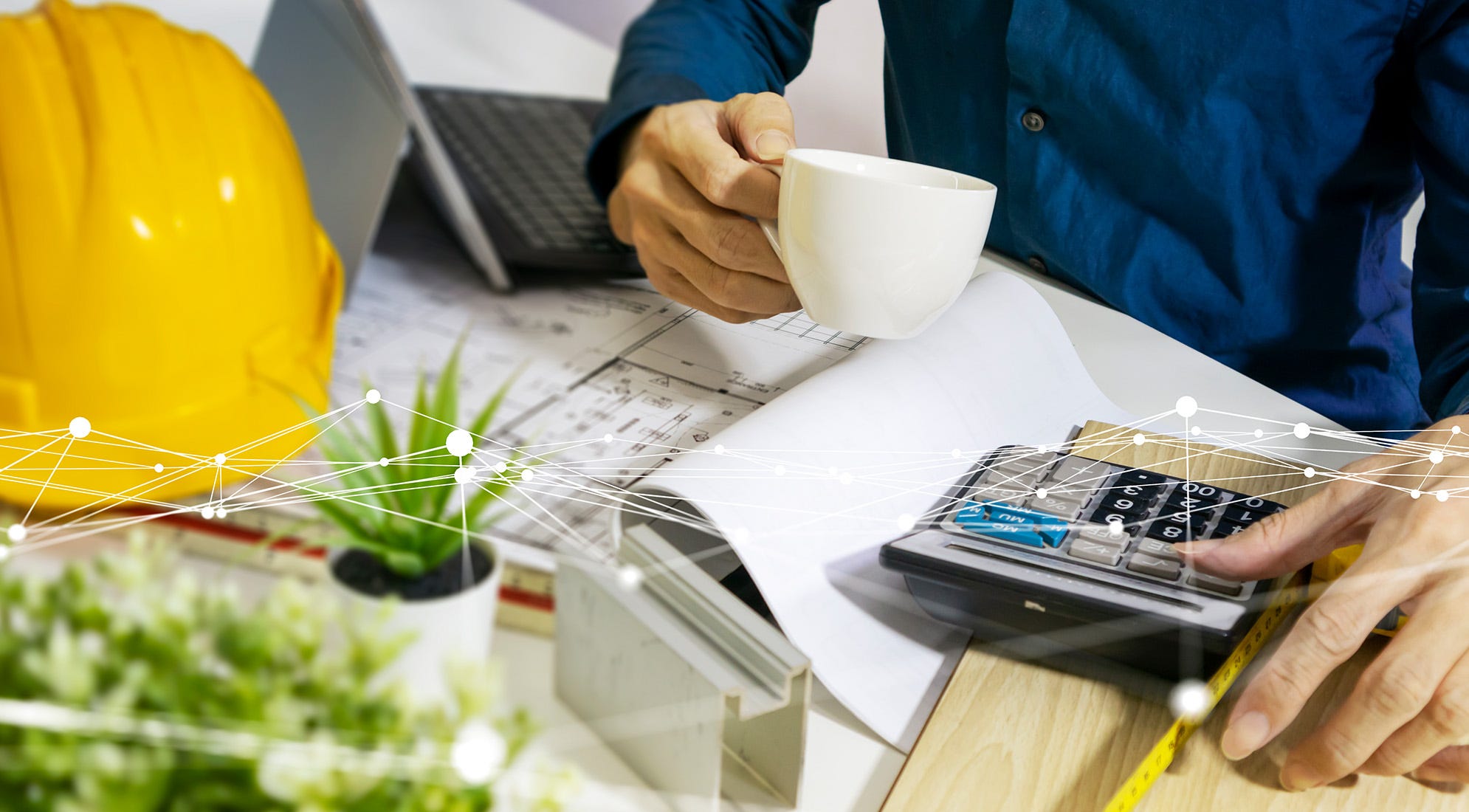
4 Hacks for Better Construction Estimates
Ask three people to draw a ranch home, and you’ll end up with three different pictures. One person may draw a brick home while the others opt for vinyl siding. Garages may face the front of the house or the side – if there’s a garage at all. All the front doors might be different colors.
Similarly, if you ask three estimators to build line-item estimates for the same project, you’re likely to end up with three different final costs. None are wrong per se, just different.
Why is that? Well, there’s not one universally-applied method for developing an accurate construction estimate. Just like drawing, estimating is a skill influenced by who you learn it from and how – and how often – you practice.
These four hacks will help you sharpen your construction estimating skills and help you create accurate estimates at an efficient pace.
Estimating Hack 1: Work from the Ground Up
A solid construction estimate starts with an accurate quantity takeoff. For estimators and contractors, that means cataloging every material, piece of equipment and labor task necessary to do the job. For some projects, like repairs and replacements-in-kind, the takeoff list might be relatively short. But for larger projects and new construction, creating this list can be a tedious uphill battle.
Luckily, there are tried-and-true practices, like breaking a project into smaller chunks, that help accelerate the takeoff process while maintaining accuracy. But it can still be easy to omit items or tasks for more complex construction work. That’s why it’s a quantity takeoff best practice to follow the actual order of construction. This typically means working from the ground up. Bottom to top – that’s the best way to go.
For projects that include multiple structures, it’s wise to create individual takeoffs for each structure to keep the numbers manageable. Even though said structures may be similar and built right next to each other, there may be significant cost difference for the materials, tasks and equipment needed to build them.
Once your quantity takeoff is complete, follow the same ground-up method for building your estimate to minimize confusion and keep the process zipping along.
Estimating Hack 2: Use Decimals, Not Fractions
For most parts of the construction process, fractions are more efficient than decimals. It would be maddening to measure and cut 2.438 feet off a board. Two and seven-sixteenths on the other hand is a no-brainer. However, the opposite is true for estimating: Using decimals will save you time and effort, especially when building your quantity takeoff.
Decimals are more precise, easier to enter into a calculator, software or spreadsheet, and generally more convenient for rounding and adding quantities. Convert any quantities or measurements that use fractions or multiple units, such as feet and inches, to single units with decimals. Stopping at two decimal places should be sufficient for your takeoff. Sticking to a simple, consistent format is key to working efficiently.
Estimating Hack 3: Have a Standard Overhead Formula
Calculating indirect costs is one of the most difficult aspects of building an estimate. This is especially true for indirect overhead costs, which may vary depending on your company’s size and location. It is best to keep standard overhead costs, graded to match a project's size and timeline before being applied to an estimate.
If your organization does not have standard overhead costs, you can use a general formula to estimate them. Add up your total overhead costs for an entire year, then divide that total by the amount of revenue you generate in an average year. Multiply the resulting percentage by the direct costs of the project. The outcome is an overhead total that you can then add to the direct costs of a project.
Estimating Hack 4: Estimate for Then, Not Now
It’s a problem as old as construction itself: Project estimates are finished months or years in advance of work beginning. Experienced estimators know this and add a reasonable margin to compensate. Even so, 98% of large construction projects still go over budget, according to the latest analysis from McKinsey & Company. Some of those projects run over budget by upwards of 80%.
Estimators who pad their estimates with a flat percentage run the risk of losing out to lower bids. Estimating for the future, particularly in times of economic volatility, requires a data-driven, scientific approach. This is a challenging thing to do, but having the right tools helps make savvy projections of future costs. One such tool is predictive cost data, available in RSMeans Data Online.
The predictive costs in our robust estimating software project future costs for any line item in our construction costs database up to three years out. Costs for tasks, materials and equipment can be accurately projected within 3% of their actual future cost, so you can keep the guesswork to a minimum.

Preparing Accurate Estimates
There’s no stopping variance in construction estimating – everyone’s drawing a different house. But having a few tools, strategies and standard processes on hand can help you work through the process better, so you can deliver for your clients at a realistic, reasonable price.